Research
Flue gas treatment
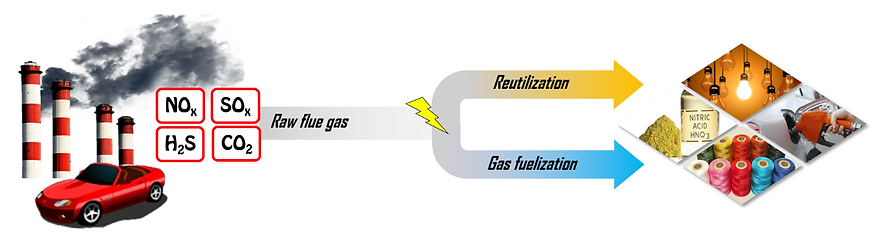
Exhaustion gases emitted from the power plants and vehicles are major causes of air pollution including acid rain and climate changes. Intensive studies have been done for the efficient removal of toxic ingredients in the emission gases, such as NOX, SOX, CO2 and H2S, before released into the air, it is also the main direction of current research. Our group, however, sees these nuisance chemicals as valuable resources and thus are attempting to convert them into value products such as nitric acid, carbonate minerals, element sulfur, and electricity. All our technologies are based on electrochemical reactions.
NOX Treatment System
NOX, mainly emitted from flue gases, causes acid rain and the depletion of the ozone layer and thus prevention of its emission is of prime importance. While several treatment technologies based on chemical and biological reactions have been developed to date, all of them have fatal drawbacks such a slow aqueous solubility of NO, difficulty in absorbent regeneration, and generation of unwanted byproducts. These drawbacks hamper the economic removal of NOX from flue gases.
A promising and more economically feasible approach is to capture and then reutilize NOX rather than to simply remove it. In fact, nitric oxide (NO) is involved in the industrial production of nitric acid as a sole intermediate.
2NO (g) + O2 (g) -> 2NO2 (g), 4NO2 (g) + O2 (g) + 2H2O (l) -> 4HNO3
If NO is selectively and purely captured from flue gases, and then reused for this purpose, the production cost of nitric acid will be greatly reduced; net positive profit may even be possible under well optimized conditions. Our ultimate goal is, therefore, to develop an innovative technology that makes it possible to capture and collect pure NO from flue gases.
Ferrous fuel cell (FC), which is our group’s unique technology, uses ferrous ion (Fe2+) as an electron donor, and oxygen (O2) as a terminal electron acceptor. Theoretical voltage production of this fuel cell is about 0.7 V under condition of pH 7 (anolyte). We have proved that ferrous-EDTA, which can keep ferrous/ferric iron in the solution and have similar redox property as free iron, substantially increases the aqueous solubility of NO by the formation of a ferrous-EDTA-NO complex. This chemical property led us to develop a FC-based NOX-capture system. In this innovative system, a NO-containing flue gas passes through a ferrous-EDTA solution, then only NO can remain in the solution with all the other gases being released. The collection of captured NOX occurs when ferrous EDTA is oxidized to ferric EDTA, which has merely weak sorption ability toward NOX. For sustainable operation of this process, consumed anolyte (ferric EDTA) is electrochemically regenerated to origin ferrous EDTA in combined another fuel cell which uses methanol anolyte and ferric EDTA catholyte. In this second fuel cell methanol serves as a fuel enabling ferric EDTA to be electrochemically reduced to ferrous form.

SOX Treatment System
Sulfur dioxide (SO2) is selected as a “Criteria Pollutant” due to its adverse effects causing various respiratory diseases and acid rain at the same time. Most SO2 emission is from energy industry, so there has a special SO2 treatment process called “Flue Gas Desulfurization”. Our approach is using electrolysis cell for handling SO2 as a form of sulfite salts by absorbing SO2 in flue gas with base solutions.
Sulfite electrolysis cell consists of anode and cathode compartments, which are separated by cation exchange membrane. Sulfite and bicarbonate salts from absorber are dissolved into anodic chamber, and sulfate salts are dissolved into cathodic chamber. Applying some voltages into electrolysis cell, sulfite is oxidized into sulfate in the anodic chamber, and proton is reduced into hydrogen gas in the cathodic chamber. During electrolysis, in the anodic chamber, the pH drop is occurred, and it lowers the solubility of bicarbonate salts, so CO2 evaporation happened. Therefore, this system suggests the way to obtain valuable products, pure H2 & CO2 gas, and dispose a pollutant, SO2, at the same time.
Additionally, we devised sulfite fuel cell in which sulfite is used as chemical energy source in anode with the help of ferric EDTA as an electron acceptor in cathode. It can work as deSOX and deNOX equipment producing electric energy. Although its power density is inadequate, it can lower the electricity consumption for the treatment of flue gas.

Electrochemical CO2 Mineralization
Mineralization is one route to take care of the ever-problematic greenhouse gas, CO2; and in so doing it can even be profitable. In this study, CO2 mineralization was realized by means of an electrochemical system, comprised of three-chambers with ion exchange membranes in-between. Carbonate-based absorbents were employed to speed up the first, rate-limiting step of CO2 hydration, and artificial seawater used as a counter-cation source. Electricity causes hydroxide ions production, via water splitting from the cathodic electrode, which pushes the carbonic acid species toward carbonate species. At the same time, electrical power drives the transport of ions, including cations in the seawater, through both ion exchange membranes, leading to the precipitation of carbonate and/or bicarbonate salts. In this way, CO2 turns into useful carbonate salts in the cathode. Also, chlorine compounds like Cl2 gas can simultaneously be produced in the anode. One more advantage of this system is that seawater, which is the cation source, is desalinated and becomes freshwater.
To further improve the performance, the distance between the electrodes was reduced so that the internal resistance was minimized. Also, several electro-catalysts, such as Pt, Ni, Cr, Co, and Mn, all of which are known to exhibit good water splitting activity, were tested, and the ones having the best catalytic activity on each electrode were selected. Desalination is also being optimized by way of introducing ion exchange resins in the middle chamber. These resins are expected to trap ions from the seawater more efficiently, and in so doing produce low salinity or even salt-free water.

H2S Treatment and Electricity Generation
Hydrogen sulfide (H2S) is present not only in crude gases but also in various industrial wastewaters. In addition, it is a byproduct from sulfate-reducing bacteria (SRB)-based wastewater treatment system, which, with an appropriate H2S treatment technology, would enable an integrated wastewater technology that far outperforms conventional aerobic microorganisms-based technology. Although a removal technology named Claus process is being widely practiced, it is energy-intensive without effective recovering energy from H2S. Therefore, the development of a sustainable technology, which enables not only to remove H2S but also to recover any value product including energy, has been the focus of recent years.
Among various types of H2S-fed fuel cell, a direct and alkaline form (so-named direct alkaline sulfide fuel cell (DASFC)) appears to be particularly advantageous in that it is operated at far milder conditions than other existing counterparts, with rather desirable oxidation kinetics in alkaline medium and without issues like anodic sulfur deposition. In light of being fed with a waste-derived liquid form of fuel, DASFC has additional and distinctive merits of easy storage and transportation.

DASFC consists of anode and cathode compartments, which are separated by cation exchange membrane. Sulfide is oxidized into sulfur oxyanion in the anodic chamber. The electricity is made when the electrons are deposited onto the anode electrode and then via external circuit transported to the cathode electrode, on which they are combined with water and oxygen to make hydroxide ion.
We are currently improving and optimizing the performance of fuel cell system by means of developing novel electro-catalysts or applying unusual catholyte other than oxygen as an electron acceptor.
Ammonia fuelization
Electrochemical Synthesis of NH3
The production of ammonia (NH3), an important fertilizer and nitrogen-compound precursor, mostly relies on the longstanding technology known as the Haber-Bosch process. Although NH3 hydrogenation is exothermic reaction but it is kinetically disfavored at ambient condition. This traditional technology is required large quantities of energy for hydrogen production, consuming over 30 GJ per ton of NH3, and releases CO2 to the atmosphere. Therefore, it is urgent to develop an alternative technology with sustainability and economical benefit.
Electrochemical NH3 synthesis process has been discussed as one of promising candidate. With this approach, energy consumption is expected to be reduced and direct carbon emission avoided compared than current method. If renewable energy could be provided to the electrochemical process, NH3 can be utilized as a green energy carrier, which has far higher energy density than any battery today can offer.
Despite these apparent advantages, electrochemical NH3 synthesis have yet to be proven sufficiently. The success of this approach should be based on the proper choice of electrolyte medium. Water, clean and abundant, has been widely used as a medium for the electrochemical reduction of N2 however low N2 solubility and faradaic efficiency are needed to improve.
We are currently examining and optimizing performance of electrochemical NH3 production system with possible substitutes.
